
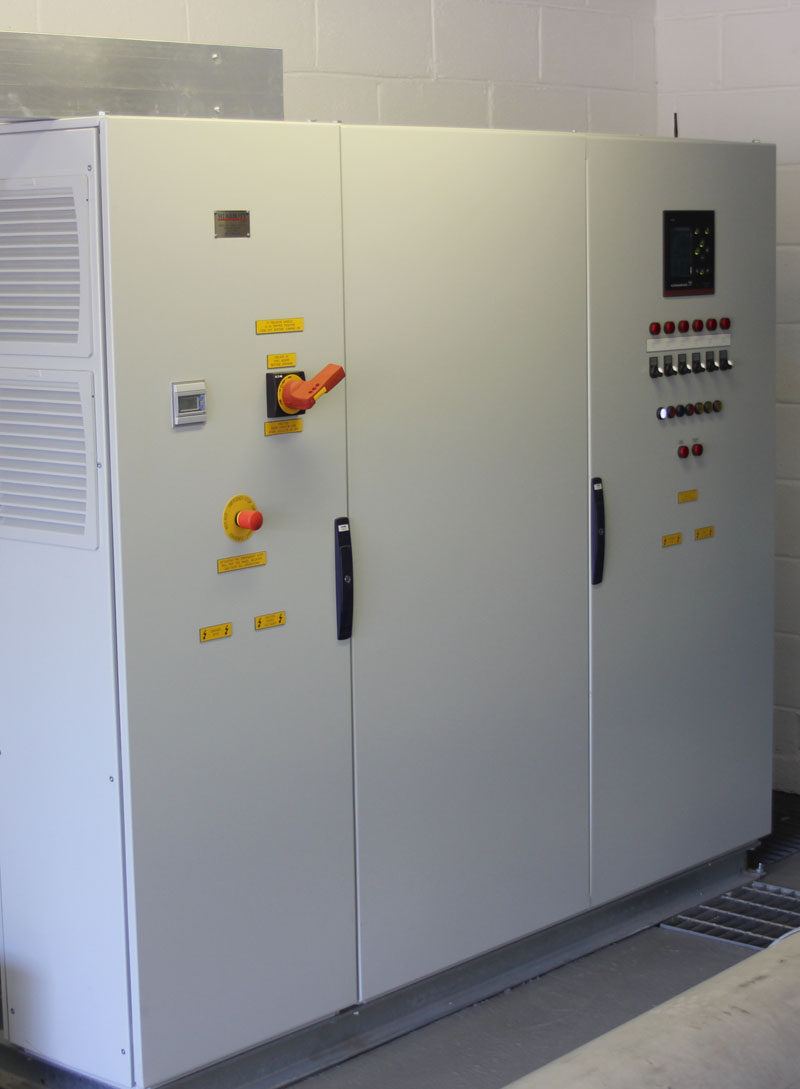
Project specification
An impressive specification to ensure sufficient capacity
The pump station consists of 5 No. Grundfos CR120-4 main duty pumps and 1 No. CRI20-8 jockey pump. The main Grundfos CR120 pumps each have a full demand duty of 115m³/hr at 8.5bar, totalling the 575m³/hr required if all of the courses are running demanding irrigation cycles. The Grundfos CRI20-8 jockey pump operates both as an initial pressure make-up pump that comes into operation prior to any of the main booster pumps, as well as being able to be called back into operation to give further assistance to the main duty pumps if the 575m³/hr requirement is marginally exceeded.
The main duty pumps each operate via dedicated 37kW Grundfos CUE Variable Frequency Drives with the jockey pump operating via a Grundfos 11kW CUE Variable Frequency Drive. The VFDs are linked via a bus network to a front end Grundfos CU352 pump control module that manages the operation of the pump station in the most efficient manner possible in order to meet the varying flow demands of the various irrigation requirements on each of the courses.
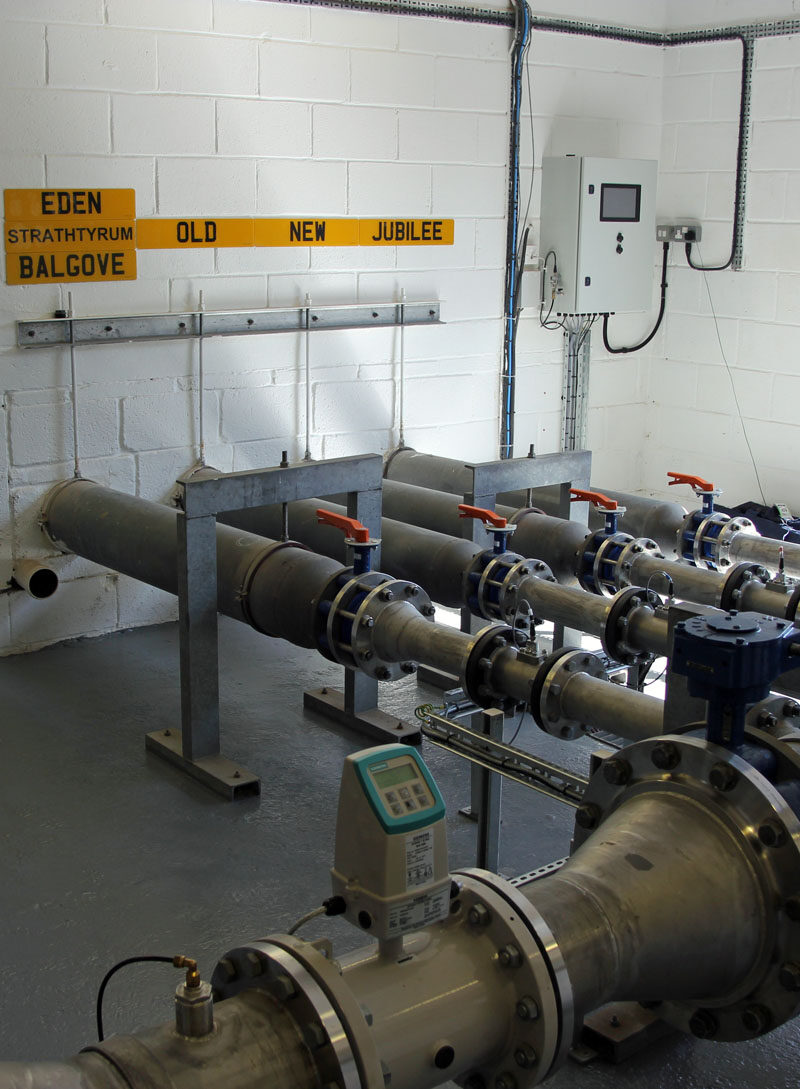
Our approach
In-house design and manufacture
The pump station design and layout was carried out in house by MJ Abbott to ensure that each component was installed as per the manufacturer’s recommendations while also allowing for the pump station to be located within the pump room in such a manner that it allowed for ease of ongoing maintenance and servicing which can sometimes be a challenge when working with pumps and ancillaries of this size.
The pump station is mounted on a bespoke galvanised chassis complete with removable galvanised tread plates to further allow for ease of maintenance when required.
All of the pipework used within the pump station is schedule 10 seam welded 304L stainless steel that offers considerable durability and longevity. The pipework was meticulously cut to length and all the weldable bends, flanges and tees were TIG welded to the required section of pipework prior to cleaning and pressure testing of each pipework assembly before it was fitted in place. The pipework ranged from the individual DN125 pump suction and discharge assemblies through to the large DN400 common suction assembly and DN350 common discharge assembly.
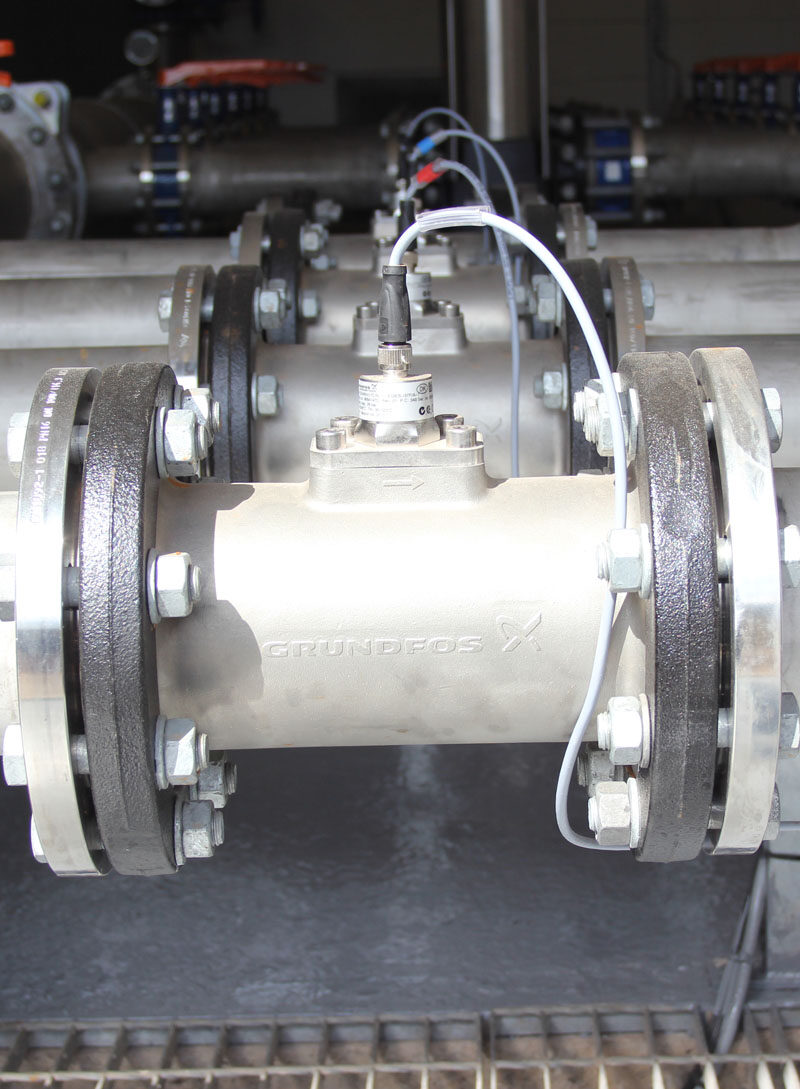
Pump control system
Flow and pressure sensors for detailed monitoring and control
Incorporated within the pipework we installed a single DN200 Siemens Mag Flo flow sensor to monitor the total pump station flow and pumped volume. In addition, 4 No. Grundfos DN100 direct vortex flow sensors are installed on the individual pipework branches that go to each of the courses to allow further dedicated flow rate and total volume figures to be monitored.
The flow and pumped volume data along with an array of data from other installed sensors within the pump station such as storage tank water level, storage tank water PH, and pump station pressure, are all available for remote viewing via the incorporation of a bespoke web-based data logging control panel that publishes both live and historic data to a custom web applet as well as a mobile phone app.
Combined with the in-built web-based feature within the Grundfos CU352 controller, this allows the monitoring of the pump station from any location that has internet connectivity. With the pump station being the heart of such a large and varied irrigation system spread over the multiple courses it was a key feature requested by the client to allow monitoring of the pump station from an off-site location.
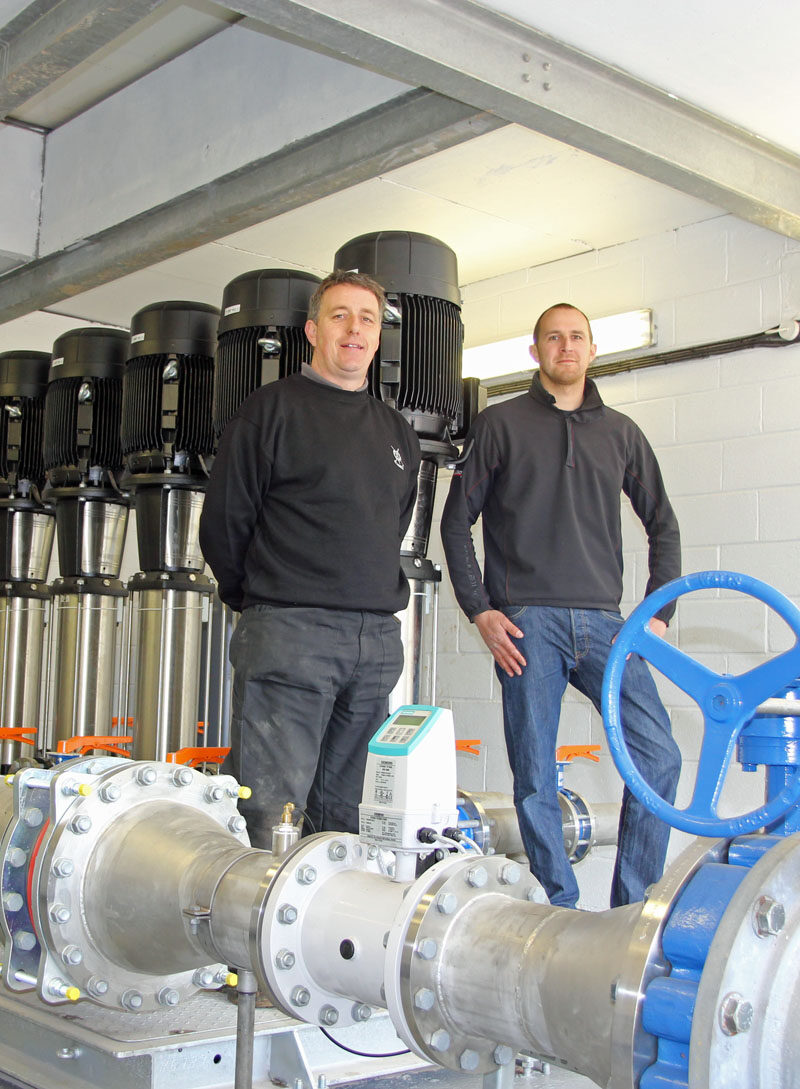
Outcomes
A reliable pump station means fewer sleepless nights
The pump station was commissioned in early 2014, with test pumping ranging from 75m³/hr through to the full 575m³/hr duty specified at the onset of the project.
The pump station ran through its first season during 2014 with a number of full 575m³/hr duty irrigation cycles without fault, restoring confidence in the pump station reliability to the client and allowing for a few more full nights’ sleep which were welcome after a number of previous years visiting site mid irrigation cycle to ensure the pump station was operating correctly.